МЕРТЕЛИ ОГНЕУПОРНЫЕ АЛЮМОСИЛИКАТНЫЕ
ТЕХНИЧЕСКИЕ УСЛОВИЯ
ГОСТ 6137-97
Предисловие
1 РАЗРАБОТАН Межгосударственным техническим комитетом по стандартизации МТК 9; Украинским Государственным научно-исследовательским институтом огнеупоров (УкрНИИО)
ВНЕСЕН Государственным комитетом Украины по стандартизации, метрологии и сертификации
2 ПРИНЯТ Межгосударственным советом по стандартизации, метрологии и сертификации (протокол № 11 от 23 апреля 1997 г.)
За принятие проголосовали:
Наименование государства |
Наименование национального органа по стандартизации |
Азербайджанская Республика
Республика Армения
Республика Беларусь
Грузия
Республика Казахстан
Киргизская Республика
Российская Федерация
Республика Таджикистан
Туркменистан
Республика Узбекистан
Украина |
Азгосстандарт
Армгосстандарт
Госстандарт Республики Беларусь
Грузстандарт
Госстандарт Республики Казахстан
Киргизстандарт
Госстандарт России
Таджикгосстандарт
Главная государственная инспекция Туркменистан
Узгосстандарт
Госстандарт Украины |
3 Постановлением Государственного комитета Российской Федерации по стандартизации и метрологии от 15 декабря 1999г. № 513-ст межгосударственный стандарт ГОСТ 6137―97 введен в действие непосредственно в качестве государственного стандарта Российской Федерации с 1 июля 2000г.
4 ВЗАМЕН ГОСТ 6137―80
5 ПЕРЕИЗДАНИЕ
1 Область применения
Настоящий стандарт распространяется на алюмосиликатные огнеупорные мертели, предназначенные для связывания алюмосиликатных изделий в огнеупорной кладке.
2 Нормативные ссылки
В настоящем стандарте использован ссылки на следующие стандарты:
ГОСТ 12.1.005―88 Система стандартов безопасности труда. Общие санитарно-гигиенические требования к воздуху рабочей зоны
ГОСТ 12.1.007―76 Система стандартов безопасности труда. Вредные вещества. Классификация и общие требования.
ГОСТ 12.8.028―76 Система стандартов безопасности труда. Респираторы ШБ-1 «Лепесток». Технические условия.
ГОСТ 12.4.041―2001 Система стандартов безопасности труда. Средства индивидуальной защиты органов дыхания фильтрующие. Общие технические требования.
ГОСТ 12.4.131―83 Система стандартов безопасности труда. Халаты женские. Технические условия.
ГОСТ 12.4.132―83 Система стандартов безопасности труда. Халаты мужские. Технические условия.
ГОСТ 17.0.0.01―76 Система стандартов в области охраны природы и улучшения использования природных ресурсов. Основные положения.
ГОСТ 17.2.3.02―78 Охрана природы. Атмосфера. Правила установления допустимых выбросов вредных веществ промышленными предприятиями.
ГОСТ 61―75 Кислота уксусная. Технические условия.
ГОСТ 83―79 Натрий углекислый. Технические условия.
ГОСТ 1770―74 Посуда мерная лабораторная стеклянная. Цилиндры, мензурки, колбы, пробирки. Общие технические условия.
ГОСТ 2226―88 (ИСО 6590-1―83, ИСО 7023―83) Мешки бумажные. Технические условия.
ГОСТ 2642.0―86 Огнеупоры и огнеупорное сырье. Общие требования к методам анализа.
ГОСТ 2642.2―86 Огнеупоры и огнеупорное сырье. Методы определения изменения массы при прокаливании.
ГОСТ 2642.4―97 Огнеупоры и огнеупорное сырье. Методы определения оксида алюминия.
ГОСТ 2642.4―97 Огнеупоры и огнеупорное сырье. Методы определения оксида железа (III).
ГОСТ 3118―77 Кислота соляная. Технические условия.
ГОСТ 3594.11―93 Глины формовочные огнеупорные. Метод определения влаги порошкообразных глин.
ГОСТ 4069―69 Огнеупоры и огнеупорное сырье. Методы определения огнеупорности.
ГОСТ 4174―77 Цинк сернокислый 7-водный. Технические условия.
ГОСТ 4206―75 Калий железосинеродистый. Технические условия.
ГОСТ 4232―74 Калий йодистый. Технические условия.
ГОСТ 4328―77 Натрия гидроокись. Технические условия.
ГОСТ 6613―86 Сетки проволочные тканные с квадратными ячейками. Технические условия.
ГОСТ 6709―72 Вода дистиллированная. Технические условия.
ГОСТ 9078―84 Поддоны плоские. Общие технические условия.
ГОСТ 10163―76 Крахмал растворимый. Технические условия.
ГОСТ 14192―96 Маркировка грузов.
ГОСТ 21650―76 Средства скрепления тарно-штучных грузов в транспортных пакетах. Общие требования.
ГОСТ 24104―88* Весы лабораторные общего назначения и образцовые. Общие технические условия.
ГОСТ 24597―81 Пакеты тарно-штучных грузов. Основные параметры и размеры.
ГОСТ 26565―85 Огнеупоры неформованные. Методы отбора и подготовки проб.
ГОСТ 27707―88 Огнеупоры неформованные. Метод определения зернового состава.
ГОСТ 29251―91 (ИСО 385-1-84) Посуда лабораторная стеклянная. Бюретки. Часть 1. Общие требования.
3 Марки
3.1 Мертели в зависимости от химико-минерального состава подразделяют на типы и марки, указанные в таблицу 1.
Таблица 1.
Тип мертеля |
Марка |
Характеристика |
Полукислый |
МП 18 |
Мертель полукислый с массовой долей Al2O3 не менее 18% |
Шамотный |
МШ 39 |
Мертель шамотный с массовой долей Al2O3 не менее 39% |
МШ 36 |
Мертель шамотный с массовой долей Al2O3 не менее 36% |
МШ 31 |
Мертель шамотный с массовой долей Al2O3 не менее 31% |
МШ 28 |
Мертель шамотный с массовой долей Al2O3 не менее 28% |
Муллитовый |
ММЛ 62 |
Мертель муллитовый с массовой долей Al2O3 не менее 62% |
Муллитокорундовый |
ММК 85 |
Мертель муллитокорундовый с массовой долей Al2O3 не менее 85% |
ММК 77 |
Мертель муллитокорундовый с массовой долей Al2O3 не менее 77% |
ММК 72 |
Мертель муллитокорундовый с массовой долей Al2O3 не менее 72% |
4 Технические требования
4.1 Мертели по физико-химическим показателям и зерновому составу должны соответствовать требованиям, указанным в таблице 2.
4.2 Мертели марок МШ 36 и МШ 31 допускается по соглашению изготовителя с потребителем изготовлять со следующим зерновым составом: проход через сетку № 2 ― не менее 100%, № 05 ― в пределах 60―94 %.
4.3 Мертели всех марок, за исключением ММК 85, изготовляются пластифицированными. Мертель марки ММК 85 пластифицируется у потребителя. Мертели МП 18, МШ39, МШ 36, МШ 31, МШ 28 и ММЛ 62 допускается по соглашению изготовителя с потребителем изготовлять без пластифицирующей добавки.
4.4 Мертели всех марок ― термотвердеющие. Мертели марок МШ 39 и МШ 36 могут изготовляться воздушно-твердеющими при введении у потребителя жидкого стекла.
4.5 Упаковка мертелей должна проводиться в бумажные битумированные мешки марок БМ или ПМ с закрытой (с клапаном) горловиной пяти- или шестислойные по ГОСТ 2226, контейнеры марок СК-2-10 или типа 1,5Л по нормативной документации. Масса нетто каждого мешка должна быть (50±1) кг.
4.6 Транспортная маркировка грузовых мест ― по ГОСТ 14192 несмываемой краской с помощью трафарета или прикреплением этикетки с обозначением:
– наименования предприятия-изготовителя;
– наименования и марки мертеля;
– обозначения настоящего стандарта;
– номер партии;
– даты изготовления мертеля.
Таблица 2.
Наименование показателя |
Норма для марки |
МП 18 |
МШ 39 |
МШ 36 |
МШ 31 |
МШ 28 |
ММЛ 62 |
ММК 85 |
ММК 77 |
ММК 72 |
Массовая доля, %:
Al2O3, не менее |
18 |
39 |
36 |
31 |
28 |
62 |
85 |
77 |
72 |
Fe2O3, не более |
― |
1,8 |
1,6 |
― |
― |
1,5 |
0,9 |
1,6 |
1,5 |
Na2CO3, в пределах |
0,12 – 0,18 |
― |
0,12 – 0,18 |
ЛСТ, в пределах |
0,07 – 0,13 |
― |
0,07 – 0,13 |
Изменение массы при прокаливании, в пределах, % |
1,3 – 3,0 |
1,3 – 3,2 |
1,3 – 3,0 |
1,8 – 3,2 |
1,3 – 3,0 |
1,5 – 3,0 |
1,2 – 1,9 |
1,6 – 3,0 |
Огнеупорность, ºС, не ниже |
1610 |
1730 |
1730 |
1690 |
1650 |
1790 |
― |
― |
― |
Массовая доля влаги, %, не более |
6 |
5 |
5 |
5 |
5 |
5 |
2 |
3 |
5 |
Зерновой состав, %, при проходе через сетку №: |
100 |
― |
― |
― |
100 |
― |
― |
― |
― |
2, не менее |
1, не менее |
― |
100 |
100 |
100 |
― |
― |
― |
― |
― |
0,5 в пределах |
60 – 94 |
― |
― |
― |
60 – 94 |
― |
― |
― |
― |
не менее |
― |
95 |
95 |
95 |
― |
100 |
100 |
100 |
100 |
009, в пределах |
― |
60 – 85 |
60 – 90 |
60 – 85 |
― |
― |
― |
― |
60 – 85 |
Не менее |
― |
― |
― |
― |
― |
70 |
70 |
70 |
― |
5 Требования безопасности
5.1 При производстве и применении алюмосиликатных мертелей вредным производственным фактором является неограниченная пыль, содержащая оксид алюминия с примесью свободных диоксида кремния и оксида железа и относящаяся к четвертому классу опасности. Предельно допускаемая концентрация (ПДК) указанной пыли в воздухе рабочей зоны производственных помещений не должна превышать 6 мг/м3 (ГОСТ 12.1.005).
5.2 Общие требования безопасности и контроля содержания вредных веществ должны соблюдаться в соответствии с требованиями ГОСТ 12.1.005, ГОСТ 12.1.007.
5.3 Острые отравления при изготовлении и применении мертелей исключены.
5.4 Мертели не образуют токсичных соединений в воздушной среде и сточных водах.
5.5 Исходные компоненты для приготовления мертелей и мертели не взрывоопасны, не горючи и не поддерживают горение.
5.6 Оборудование, используемое для приготовления мертелей, должно быть герметизировано и снабжено аспирационными устройствами. Места возможного пыления должны орошаться водой. Должна проводиться влажная уборка складских и производственных помещений с применением индивидуальных средств защиты ― противопылевых респираторов типа ШБ-1 «Лепесток» по ГОСТ 12.4.028 и фильтрующих по ГОСТ 12.4.041.
5.7 Все работающие должны быть обеспечены спецодеждой (ГОСТ 12.4.131, ГОСТ 12.4.132) и средствами защиты ― очками и противопылевыми респираторами.
Должны соблюдаться правила личной гигиены: обязательное ношение спецодежды, мытье рук перед приемом пищи, прием пищи в специальных помещениях.
Периодически, не реже одного раза в год, должны проводиться медицинские осмотры работающих.
5.8 При производстве и применении мертелей должна соблюдаться система стандартов по охрани окружающей среды ― ГОСТ 17.0.0.01, ГОСТ 17.2.3.02.
6 Правила приемки
6.1 Мертели предъявляют к приемке партиями. Партия должна состоять из мертеля одной марки и сопровождаться одним документом о качестве, содержащим:
– наименование предприятия-изготовителя;
– товарный знак;
– марку мертеля;
– номер партии;
– массу партии;
– результаты лабораторных испытаний;
– обозначение настоящего стандарта.
Масса партии мертеля ― не более 150 т.
6.2 Предприятия-изготовители и потребители проводят приемосдаточные испытания мертелей марок МП 18, МШ 39, МШ 31, МШ 28 от каждой третьей партии, остальных марок ― от каждой партии.
6.3 Для проверки качества мертелей отбирают выборку по ГОСТ 26565.
6.4 При получении неудовлетворительных результатов испытаний хотя бы по одному из показателей по нему проводят повторные испытания на удвоенной выборке, взятой от той же партии. Результаты повторных испытаний распространяются на всю партию.
7 Методы испытаний
7.1 Отбор и подготовку проб мертелей проводят по ГОСТ 26565.
7.2 Массовую долю Al2O3, Fe2O3и измерение массы при прокаливании определяют по ГОСТ 2642.0, ГОСТ 2642.2, ГОСТ 2642.4 и ГОСТ 2642.5, а массовую долю Na2CO3 и ЛСТ ― по методике, приведенной в приложении А. Допускается применение других методов анализа, обеспечивающих требуемую точность определения.
При возникновении разногласий в оценке качества мертелей определения проводят по ГОСТ 2642.2, ГОСТ 2642.4, ГОСТ 2642.5 и приложению А (контрольные методы).
7.3 Огнеупорность определяют по ГОСТ 4069.
7.4 Массовую долю влаги определяют по ГОСТ 3594.11 или другими методами анализа, обеспечивающими требуемую точность определения. Контрольный метод ― по ГОСТ 3594.11.
7.5 Зерновой состав определяют с помощью набора сит с сетками № 2, 1, 05 и 009 (ГОСТ 6613) по ГОСТ 27707 методом комбинированного рассева.
7.6 Контроль ПДК пыли алюмосиликатных мертелей в воздухе рабочей зоны производственных помещений производится в соответствии с нормативной документацией.
8 Транспортирование и хранение
8.1 Транспортирование мертелей осуществляется в контейнерах типа 1,5Л или типа СК-2-10 по нормативной документации, а мертелей, упакованных в мешки, — пакетами по нормативной документации в крытых железнодорожных вагонах. Пакетирование в транспортные пакеты проводят с помощью средств скрепления по ГОСТ 21650 на плоских поддонах по ГОСТ 9078. Габаритные размеры пакета — по ГОСТ 24597. Транспортирование мертелей осуществляется в соответствии с правилами перевозки грузов и техническими условиями погрузки и крепления грузов, утвержденными МПС. По соглашению изготовителя с потребителем допускается перевозить мертели навалом в полувагонах.
8.2 В графу «Особые заявления и отметки отправителя» железнодорожных накладных, которые
направляются вместе с грузом потребителю, заносятся следующие обозначения:
– наименование мертеля;
– марка мертеля;
– обозначение настоящего стандарта.
8.3 Хранение мертелей осуществляется в крытых складах, бункерах или контейнерах изготовителя или потребителя в условиях, исключающих увлажнение и засорение материалами другого со
става. Срок хранения мертелей — не более 12 мес. со дня изготовления.
ПРИЛОЖЕНИЕ А
(обязательное)
Методика определения массовой доли лигносульфоната (ЛСТ) и углекислого натрия (Na2CO3) в алюмосиликатных мертелях АЛ Определение массовой доли ЛСТ (при массовой доле ЛСТ от 0,05 до 0,15 % в пробе мертеля)
Метод основан на окислении в щелочном растворе присутствующих в ЛСТ продуктов гидролиза пенто-занов (ксилозы) и гексозанов (маннозы, глюкозы, галактозы) железосинеродистым калием К3 [Fe(CN)6] и йодометрическим титрованием избытка железосинеродистого калия.
АЛЛ Аппаратура, реактивы, растворы
Весы лабораторные общего назначения по ГОСТ 24104 с разновесами 2-го класса точности с наибольшим пределом взвешивания до 200 г или любые другие весы, отвечающие по своим метрологическим характеристикам требованиям ГОСТ 24104.
Шкаф сушильный с терморегулятором, обеспечивающий нагрев до температуры 150—200 °С.
Посуда мерная (колбы, цилиндры) по ГОСТ 1770.
Приборы мерные (бюретки, пипетки) по ГОСТ 29251.
Натрий углекислый по ГОСТ 83, раствор массовой концентрации 0,01 г/см3.
Натрия гидроксид по ГОСТ 4328, раствор молярной концентрации эквивалента 2 моль/дм3.
Цинк сернокислый 7-водный по ГОСТ 4174, раствор массовой концентрации 0,04 г/см3.
Калий железосинеродистый 3-водный по ГОСТ 4206, раствор массовой концентрации 0,01 г/см3.
Калий йодистый по ГОСТ 4232, раствор массовой концентрации 0,1 г/см3.
Крахмал растворимый по ГОСТ 10163, раствор массовой концентрации 0,005 г/см3.
Кислота уксусная по ГОСТ 61, раствор массовой концентрации 0,7 г/см3.
Раствор тиосульфата натрия (серноватистокислого натрия), по нормативной документации молярной концентрации эквивалента 0,02 моль/дм3; готовят разбавлением раствора молярной концентрации эквивалента 0,1 моль/дм3.
Вода дистиллированная по ГОСТ 6709.
Раствор концентрата ЛСТ, готовят следующим образом: 2 г концентрата ЛСТ марки А взвешивают на лабораторных весах, смывают навеску в мерную колбу вместимостью 500 см3, разбавляют водой до метки и перемешивают. Массовую концентрацию раствора ЛСТ С, г/см3, вычисляют по формуле
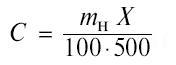
где тн — масса навески концентрата ЛСТ, г;
X — массовая доля сухого вещества ЛСТ (в зависимости от плотности концентрата ЛСТ определяется по НД), %.
Массовая концентрация раствора тиосульфата натрия по ЛСТ определяется следующим образом: в конусную колбу вместимостью 250 см3 наливают из бюретки 5 см3 раствора ЛСТ, 50 см3 раствора углекислого натрия, 10 см3 раствора гидроксида натрия и 10 см3 раствора сернокислого цинка. Доводят раствор в колбе до кипения. Доливают из бюретки 10 см3 раствора железосинеродистого калия и кипятят в течение 5 мин для окисления редуцирующих веществ. Избыток К3 [Fe(CN)6] определяют следующим образом: охлаждают колбу в воде, приливают 10 см3 раствора йодистого калия и 7 см3 уксусной кислоты, перемешивают и титруют выделившийся йод раствором тиосульфата натрия в присутствии 1—2 см3 раствора крахмала:
2К3 [Fe(CN)6] + 2KJ = 2К4 [Fe(CN)6] + 2J;
2J + 2Na2S2O3 = Na2S4O6 + 2NaJ.
Конец титрования определяют по исчезновению синей окраски раствора.
Одновременно с окислением 5 см3 раствора ЛСТ проводят контрольный опыт для определения расхода тиосульфата натрия в отсутствии ЛСТ.
В контрольном опыте используют такое же количество реактивов, как для определения массовой концентрации, и отмечают количество тиосульфата натрия (V1), см3.
Массовую концентрацию раствора тиосульфата натрия С1, выраженную в г/см3 ЛСТ, вычисляют по формуле
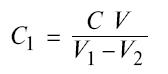
где С — массовая концентрация раствора ЛСТ, взятого для титрования, г/см3;
V— объем раствора ЛСТ, взятого для титрования, см3;
V1— объем раствора тиосульфата натрия, израсходованного на титрование при контрольном опыте, см3;
V2— объем раствора тиосульфата натрия, израсходованного на титрование раствора ЛСТ, см3.
А. 1.2 Проведение анализа
5—10 г мертеля взвешивают, помещают в стакан вместимостью 100 см3, приливают 10 см3 раствора углекислого натрия, перемешивают в течение 2 мин и отфильтровывают на воронке Бюхнера под вакуумом через фильтр (белая лента) диаметром 9 см.
Осадок на фильтре промывают 2 раза 20 см3 воды и переводят фильтрат в коническую колбу вместимостью 250 см3.
Приливают 10 см3 раствора гидроксида натрия, 10 см3 раствора сернокислого цинка, нагревают до кипения и добавляют из бюретки 10 см3 раствора железосинеродистого калия. Кипятят в течение 5 мин, охлаждают, добавляют 10 см3 раствора йодистого калия и 7 см3 уксусной кислоты и титруют выделившийся йод раствором тиосульфата натрия в присутствии 1—2 см3 раствора крахмала до исчезновения синей окраски.
А. 1.3 Обработка результатов
Массовую долю ЛСТ в мертеле Xv %, вычисляют по формуле
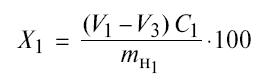
где V1 — объем раствора тиосульфата натрия, израсходованного на титрование при контрольном опыте, см3;
V3— объем раствора тиосульфата натрия, израсходованного на титрование навески мертеля, см3; C1 — массовая концентрация тиосульфата натрия, выраженная в г/см3 ЛСТ;
mи1 — масса навески мертеля, г.
Абсолютные расхождения результатов двух параллельных определений (при доверительной вероятности 0,95) не должны превышать допускаемого значения 0,020 %.
А.2 Определение массовой доли Na2CO3 (при массовой доле Na2CO3 от 0,06 до 0,20 %)
А.2.1 Аппаратура, реактивы
Весы лабораторные общего назначения по ГОСТ 24104, 2-го класса точности с наибольшим пределом взвешивания до 200 г или другие весы, отвечающие по своим метрологическим характеристикам требованиям ГОСТ 24104.
Кислота соляная по ГОСТ 3118, раствор молярной концентрации 0,1 моль/дм3.
Метиловый оранжевый, раствор массовой концентрацией 0,002 г/см3 по нормативной документации.
Вода дистиллированная по ГОСТ 6709.
А.2.2 Проведение анализа
10 г мертеля взвешивают, обрабатывают 50 см3 воды, фильтруют под вакуумом. Приливают к фильтрату 5—6 капель метилового оранжевого и титруют раствором соляной кислоты до появления розовой окраски.
А.2.3 Обработка результатов
Массовую долю Na2CO3 в мертеле X, %, вычисляют по формуле
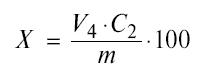
где V4 — объем раствора соляной кислоты, израсходованного на титрование, см3;
С2 — массовая концентрация раствора соляной кислоты, выраженная в г/см3 Na2CO3;
m— масса навески мертеля, взятого для определения Na2CO3.
Абсолютные расхождения результатов двух параллельных определений (при доверительной вероятности Р = 0,95) не должны превышать допускаемого значения 0,020 %.